Automatic container loadin system (equipped with AMR tracked vehicle)
The device uses a 3D camera to scan the stack and the production point cloud data calculates the spatial coordinates of the top surface of the box. The depalletizing robot accurately depalletizes the box based on the spatial coordinates of the top surface of the box. The 3D camera can also scan and identify whether the top surface of the box is damaged or contaminated. The 6-axis robot is used to depalletize the stack, turn the product 90 ° and place it. The depalletizing gripper can realize different box numbers grabbing, such as 2 or 3 boxes, according to the stack type. It can achieve an automated solution of automatic depalletizing, automatic pallet recycling, and automatic box output. Afterwards, when the AMR vehicle autonomously navigates through SLAM lidar navigation and constantly corrects the body posture, the AMR vehicle can finally be centered into the carriage. The 3D camera on the AMR vehicle scans the spatial data of the carriage and feeds back the spatial coordinates of the right bottom corner of the carriage head to the loading robot. The loading robot grabs the boxes and palletizes them based on the corner coordinates. The 3D camera scans the coordinates of the boxes stacked by the robot each time and calculates the corner points. It calculates whether there will be collisions and whether the boxes are tilted or damaged during each loading. The robot corrects the loading posture based on the calculated corner point data. After the robot palletizes one side, the AMR vechile retreats a predetermined distance to load the next row. It continuously loads and retreats until the carriage is filled with boxes. The AMR vehicle is exit out of carriage and waits for the next carriage to load boxes.
The complete packing system layout
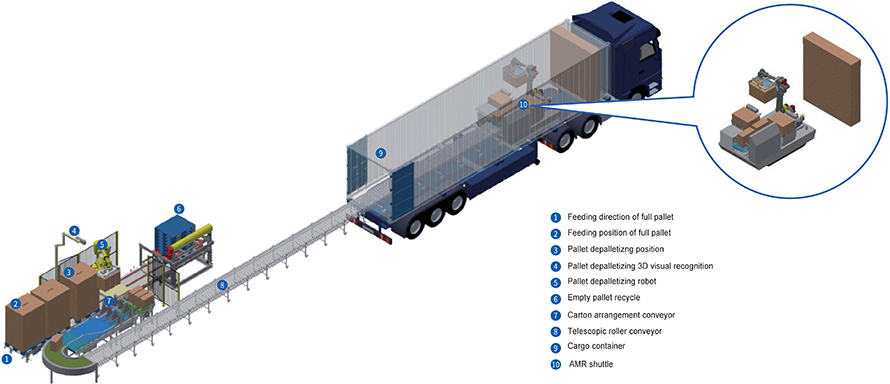
Main configuration
Robot arm | ABB/KUKA/Fanuc |
Motor | SEW/Nord/ABB |
Servo motor | Siemens/Panasonic |
VFD | Danfoss |
Photoelectric sensor | SICK |
Touch screen | Siemens |
Low voltage apparatus | Schneider |
Terminal | Phoenix |
Pneumatic | FESTO/SMC |
Sucking disc | PIAB |
Bearing | KF/NSK |
Vacuum pump | PIAB |
PLC | Siemens /Schneider |
HMI | Siemens /Schneider |
Chain plate/chain | Intralox/rexnord/Regina |
Main structure description
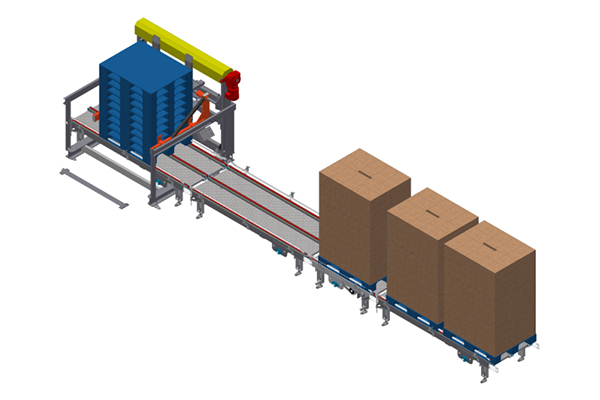
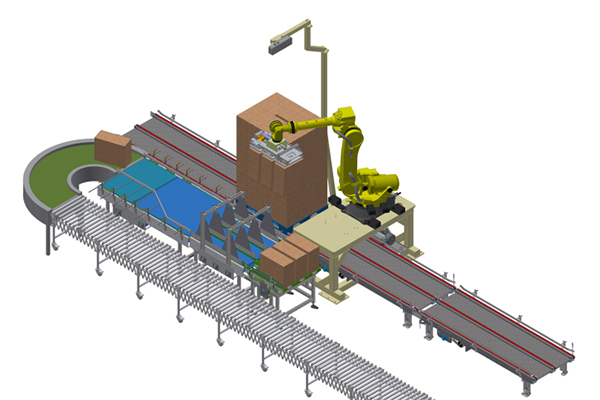
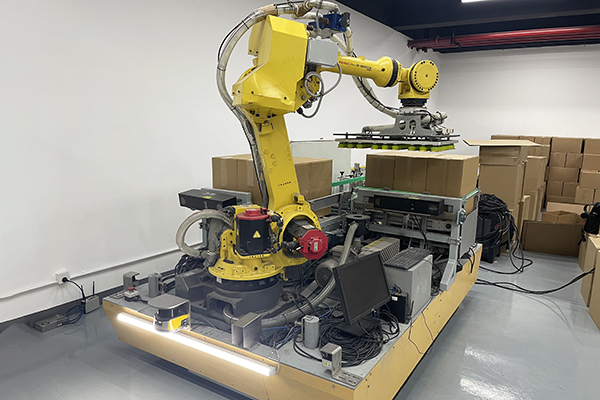
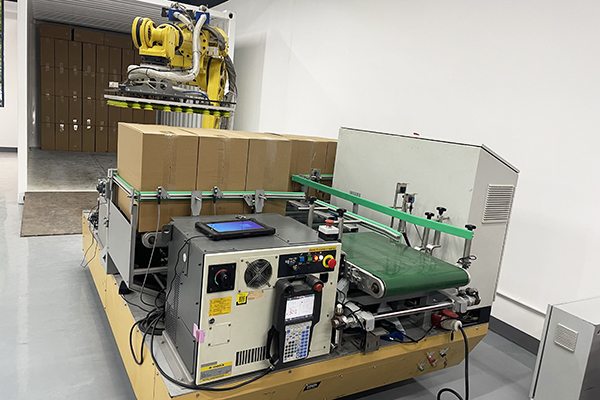